Rubber Roof Repair
Durable, Cost-Effective Repairs for EPDM and Flat Roofs
Rubber roofs—also known as EPDM (Ethylene Propylene Diene Monomer) roofing—are a popular choice for flat and low-slope roofs across Dallas. They’re flexible, energy-efficient, and typically last decades when properly maintained. But like any roofing material, they can develop leaks, cracks, bubbles, and shrinkage over time.
At Dallas Roof Repair Co., we help homeowners and property managers find experienced local contractors who specialize in diagnosing and repairing rubber roofs. Whether it’s a small patch, seam reseal, or full membrane replacement, we connect you with professionals who know how to get the job done right the first time.
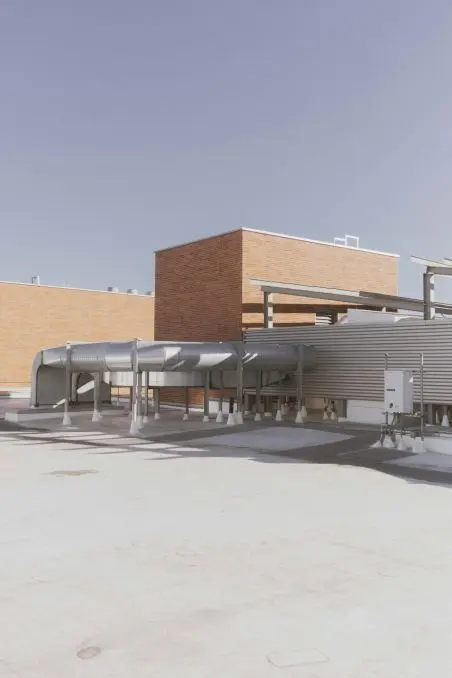
Common Issues with Rubber Roofs
Fixing a rubber roof issue early can help you avoid the high cost of structural damage or full replacement. Some of the biggest advantages include:
Rubber roofs are known for their resilience and affordability, but they’re still susceptible to the effects of weather, age, and poor installation. When caught early, most problems can be repaired without needing to replace the entire roof.
Here are some of the most common rubber roofing issues:
1. Seam Separation
EPDM roofing is typically installed in large sheets, joined together with adhesive at the seams. Over time, exposure to sun and weather can cause the seams to loosen or peel apart, allowing water to seep in.
2. Punctures and Tears
Foot traffic, debris, tree branches, or hail can cause small tears or punctures in the rubber membrane. These are often easy to miss until water damage appears inside the structure.
3. Shrinkage
As rubber roofing ages, it can shrink slightly—pulling away from edges, flashing, or vents. Shrinkage is a common cause of roof edge failures and water infiltration.
4. Blistering and Bubbling
Trapped moisture or improper adhesion can cause raised bubbles to form beneath the membrane. These blisters may rupture over time, leading to leaks.
5. Ponding Water
Flat roofs often suffer from poor drainage. If water is allowed to sit for more than 48 hours, it can strain the membrane, weaken adhesive bonds, and cause premature breakdown.
6. UV Damage
Although EPDM is UV-resistant, long-term sun exposure can cause chalking, brittleness, and surface degradation if not properly maintained.
What’s Involved in Rubber Roof Repair?
The right repair approach depends on the type and extent of damage, the age of the roof, and how well it was installed originally. The contractors we help you connect with are skilled in diagnosing and performing all types of EPDM and rubber roofing repairs.
Here’s what a typical rubber roof repair might include:
Inspection and Damage Assessment
A thorough inspection includes checking for seam integrity, punctures, pooling water, substrate damage, and potential causes of internal leaks.
Cleaning and Surface Preparation
The area surrounding the damage is cleaned of dirt, debris, and moisture to ensure proper adhesion of new patches or sealant.
Patch Application
Punctures and small tears are repaired with rubber membrane patches, typically applied with EPDM-compatible adhesive or heat-welding equipment.
Seam Resealing
Separated seams are either re-glued or heat-sealed, depending on the age of the roof and the type of adhesive originally used.
Edge and Flashing Repairs
If shrinkage or UV damage has pulled the membrane away from parapet walls, chimneys, or vents, flashing is reset or replaced, and new membrane may be added to restore a watertight seal.
Protective Coatings
In some cases, contractors may apply a UV-resistant elastomeric or silicone coating to extend the life of the roof and protect vulnerable areas from further exposure.
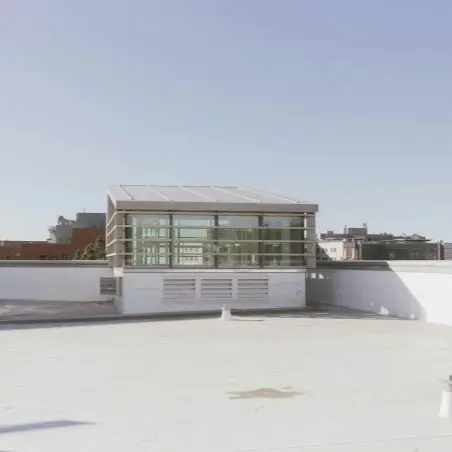
Signs Your Rubber Roof Needs Repair
Unlike pitched shingle roofs, rubber roofing issues are often harder to spot from the ground. Here are some signs you might need a rubber roof repair:
- Water stains on interior ceilings or walls
- Visible bubbles or raised areas on the membrane
- Peeling seams or adhesive
- Cracks around skylights, vents, or flashing
- A musty odor in your attic or upper rooms
- Loose or lifted edges of the membrane
If you notice any of these warning signs, it’s best to get a professional inspection to determine the extent of the issue—and stop it from spreading.
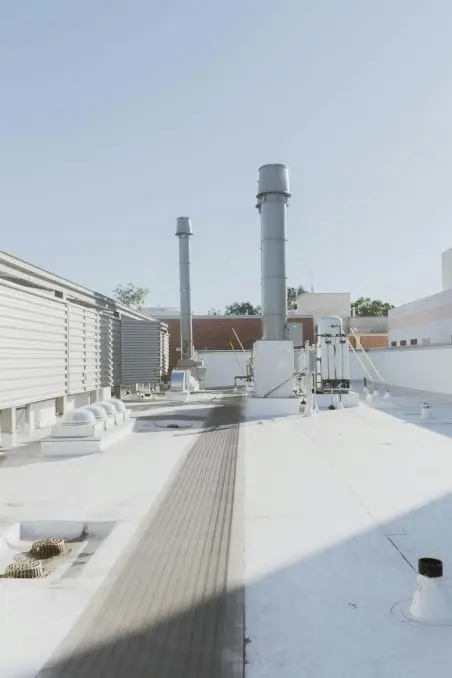
When Does a Rubber Roof Need Replacement Instead of Repair?
While many rubber roofing issues are repairable, there are situations when replacement is the more cost-effective long-term solution. A reputable contractor will help you weigh your options honestly and transparently.
You may need a replacement if:
- The roof is more than 20–25 years old
- Punctures or cracks are widespread
- Moisture has seeped into insulation or decking
- Membrane shrinkage has caused permanent deformation
- Repairs are more frequent and costly than before
- You’re planning to sell the property and want peace of mind
A qualified roofer can tell you if a repair will buy you another 5–10 years—or if it’s time to consider a full re-roof.
Why Homeowners Choose Dallas Roof Repair Co.
Dallas Roof Repair Co. is your connection to qualified, local contractors who specialize in repairing rubber roofing systems. Whether your home has a flat garage roof, a low-slope addition, or a full commercial EPDM roof, we help you find professionals who can fix the problem fast.
Service Areas in Dallas
- Dallas
- Fort Worth
- Arlington
- Plano
- Irving
- Garland
- Frisco
- McKinney
- Grand Prairie
- Denton
- Mesquite
- Carrollton
- Lewisville
- Richardson
- Allen
Don’t Let a Rubber Roof Leak Drain Your Wallet
Rubber roofs are tough—but they’re not indestructible. If you notice bubbling, sagging, or staining, don’t wait. The sooner you act, the less likely you’ll face interior water damage, structural issues, or a full roof replacement.
Dallas Roof Repair Co. helps you get the problem repaired quickly, affordably, and by the right people—no sales pressure, just trusted connections.